Every year, pool, spa and hearth retailers and business owners alike, come face-to-face with the task of having to conduct physical counts. Conducting a physical count can be a long, pain-staking process if you and your team are not prepared. Below are some best practice techniques that can help you conduct a speedy and efficient physical count.
Prior to the Physical Count
- Plan a meeting with your team ahead of time to go over the process. In this meeting, you should create two-man teams to count the inventory. You can assign each team to specific bin locations. If you have inventory spread throughout multiple stock sites, you can assemble specific teams to each stock site to conduct the count. The plan here is to have one person count the inventory while the other team member collects the data either manually on count sheets or with a barcode scanner. Breaking the count into small groups eliminates your team members from becoming too overwhelmed at the thought of having to count thousands of items.
- Review any open transactions such as items on open orders, un-received items on purchase orders or items in transit between locations. for the items that are selected for the count. If you’re lucky, your business management software will list these transactions for you.
- Remove any defective items from your inventory so they are not part of the count.
- Make sure you are closed during the days you are conducting your physical counts. Conducting business during this time can cause discrepancies in your count.
Time to Start Counting!
When the counts are being completed, have your Inventory manager verify the counts. It’s best to start with your items that are your fast sellers and bring in the most revenue., These items can contain the most counting errors because of their turnover rate. Your business management software should be able to filter the count by fast moving items to expedite the count process.
As soon as the counts are verified, enter them into a spreadsheet or upload the data into your inventory tracking system via your barcode scanner.
Prior to completing the count, review all data entered for discrepancies to avoid having to conduct a second or third count.
Once the count is complete, hold another team meeting to discuss the process and procedures. Discuss what worked, what didn’t, and what you could change for future counts. The whole point here is to get ideas on how to make your next count smoother.
- Adrian Amposta
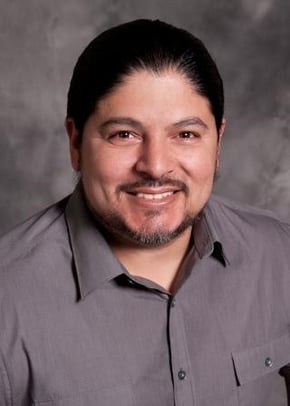